Quality test method (qtm) testing
Time Estimate: Typically 15 – 22 days from oncoming of testing
The Standard Test Method (QTM) may be the full test method accustomed to verify comprehensive product performance and quality. Is a result of QTM testing are utilized to determine whether an item has met the standard Standards. Random choice of the merchandise samples that should be delivered to the exam lab is needed and should be arranged ahead of time through Lighting Global.
- Pico-solar products (products with peak power rating of 10W or fewer) are tested based on the new edition of IEC/TS 62257-9-5. This along with other key IEC documents for rural electrification are presently available for a cheap price for qualified stakeholders. Tests for pico-solar products make use of a sample size six. As many as a minimum of 18 product samples, selected from the stock with a minimum of 500 units, is going to be needed for QTM testing. [If additional exams are needed or even the manufacturer demands that mechanical durability tests be conducted on unaltered samples, additional samples might be selected.]
- Solar home system kits, which for that purpose of Lighting Global are products with peak power ratings greater 10 W as much as 350 W, are tested based on the new edition of IEC/TS 62257-9-5. Tests for SHS kits make use of a sample size four. As many as a minimum of 16 product samples, selected from the stock with a minimum of 200 units, is going to be needed for QTM testing. [If additional exams are needed or even the manufacturer demands that mechanical durability tests be conducted on unaltered samples, additional samples might be selected.]
NOTE: In June 2018 the Worldwide Electrotechnical Commission (IEC) printed a re-creation from the test methods employed for testing solar products, IEC 62257-9-5:2018 (also written as IEC 62257-9-5 erectile dysfunction. 4). We’ll phase being used of those new methods between June – December 2018. This stakeholder memo describes the connected changes and expected timelines. Also, if you are looking at acquiring the latest version from the test methods, first determine should you qualify to renegotiate deals about this along with other key IEC documents.
Step One: Inform the sunlight Global Quality Assurance Group of your curiosity about testing your products(s) while using QTM method.
Step Two: The QA team looks at the information provided within the Manufacturer Information Form in addition to needed documentation. This requirement is described within the Initial Engagement stage from the Testing Process.
Step Three: The QA team follows track of you to definitely determine a suitable test plan.
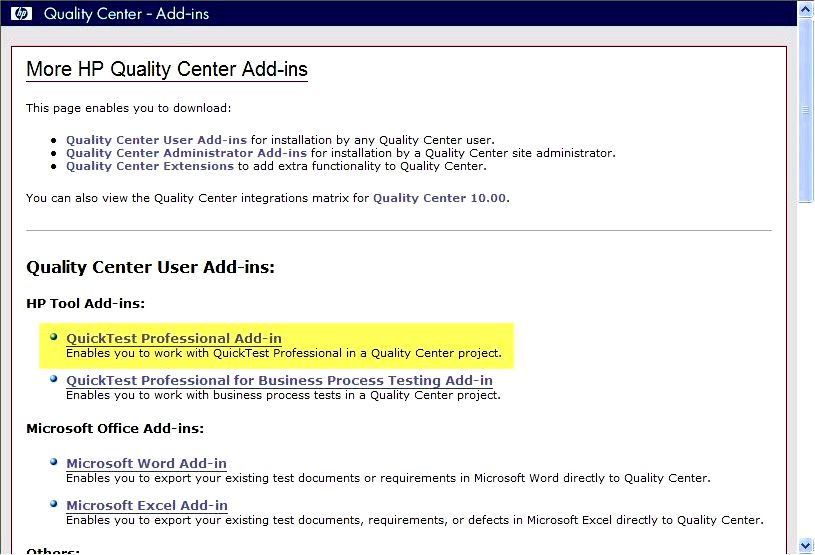
Note that you are requested to explain and/or provide more details, as needed.
Step Four: The QA team transmits draft Independent Testing Deal for review. The Independent Testing Agreement includes the exam plan, and also the contact details for a summary of approved test labs.
Step Five: After you have informed the QA team you have NO OBJECTIONS towards the Test Agreement, your final version is distributed for signature. The e-mail may also have a connect to the Random Sampling Form as well as an invoice for that program charges connected using the following services: test coordination, random sampling, report reviews, and reporting.
Observe that these types of services typically ended up costingDollar 1000, but might increase with respect to the logistics connected with random sampling. This cost doesn’t range from the testing charges, that are based on the exam lab.
Step Six: In parallel, you have to choose an authorized test lab for QTM testing by Lighting Global, and see using the lab aspects like availability and price of testing. To learn more, please review their list of approved test labs and also the Test Lab Policy.
Step 7: Return a signed copy from the Testing Agreement towards the QA team.
Observe that Random Sampling and Testing may start as we have obtained your completed Manufacturer Information Form along with a signed Test Agreement.
Step 8: Begin the payment procedure for the Program’s fee invoice and inform the QA team.
Observe that final testing recent results for your products(s) are only sent as we have confirmed payment of these charges.
Step 9: Complete the Random Sampling Form. This type asks that you simply: (A) Identify the specific test lab you’re considering to check your products(s), (B) Provide contact details for sampling, (C) Provide street address for that sampling location, and (D) Give a time frame for sampling.
Observe that finishing this type works as a confirmation that you’ll satisfy the minimum stock needs throughout the provided some time and location. Therefore, it’s very essential that all the details is finished and accurate.
Step 10: In parallel, your organization and also the lab must enter agreement for testing.
Observe that contracting and payment of testing charges is handled between your test lab.
Time Estimate: Typically 15 – 22 days from oncoming of testing
The Standard Test Method (QTM) may be the full test method accustomed to verify comprehensive product performance and quality. Is a result of QTM testing are utilized to determine whether an item has met the standard Standards. Random choice of the merchandise samples that should be delivered to the exam lab is needed and should be arranged ahead of time through Lighting Global.
- Pico-solar products (products with peak power rating of 10W or fewer) are tested based on the new edition of IEC/TS 62257-9-5. This along with other key IEC documents for rural electrification are presently available for a cheap price for qualified stakeholders. Tests for pico-solar products make use of a sample size six. As many as a minimum of 18 product samples, selected from the stock with a minimum of 500 units, is going to be needed for QTM testing. [If additional exams are needed or even the manufacturer demands that mechanical durability tests be conducted on unaltered samples, additional samples might be selected.]
- Solar home system kits, which for that purpose of Lighting Global are products with peak power ratings greater 10 W as much as 350 W, are tested based on the new edition of IEC/TS 62257-9-5. Tests for SHS kits make use of a sample size four. As many as a minimum of 16 product samples, selected from the stock with a minimum of 200 units, is going to be needed for QTM testing. [If additional exams are needed or even the manufacturer demands that mechanical durability tests be conducted on unaltered samples, additional samples might be selected.]
NOTE: In June 2018 the Worldwide Electrotechnical Commission (IEC) printed a re-creation from the test methods employed for testing solar products, IEC 62257-9-5:2018 (also written as IEC 62257-9-5 erectile dysfunction. 4). We’ll phase being used of those new methods between June – December 2018. This stakeholder memo describes the connected changes and expected timelines. Also, if you are looking at acquiring the latest version from the test methods, first determine should you qualify to renegotiate deals about this along with other key IEC documents.
Step One: Inform the sunlight Global Quality Assurance Group of your curiosity about testing your products(s) while using QTM method.
Step Two: The QA team looks at the information provided within the Manufacturer Information Form in addition to needed documentation. This requirement is described within the Initial Engagement stage from the Testing Process.
Step Three: The QA team follows track of you to definitely determine a suitable test plan.
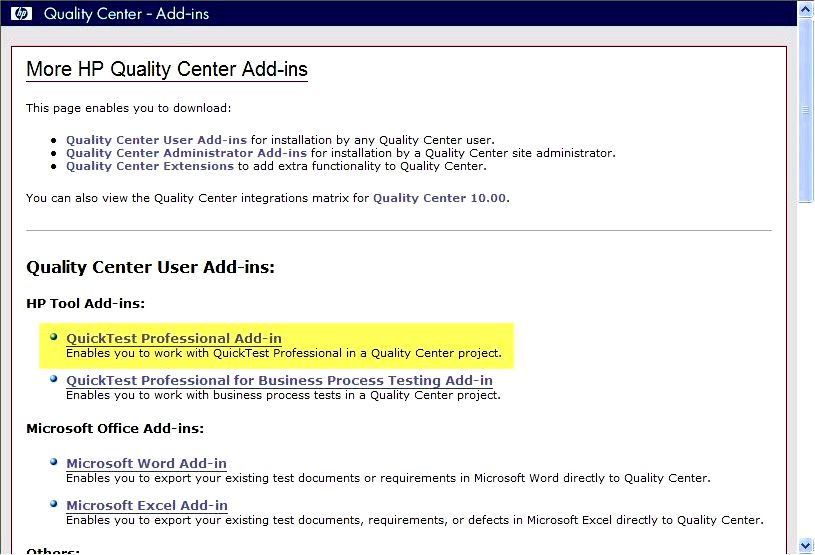
Note that you are requested to explain and/or provide more details, as needed.
Step Four: The QA team transmits draft Independent Testing Deal for review. The Independent Testing Agreement includes the exam plan, and also the contact details for a summary of approved test labs.
Step Five: After you have informed the QA team you have NO OBJECTIONS towards the Test Agreement, your final version is distributed for signature. The e-mail may also have a connect to the Random Sampling Form as well as an invoice for that program charges connected using the following services: test coordination, random sampling, report reviews, and reporting.
Observe that these types of services typically ended up costingDollar 1000, but might increase with respect to the logistics connected with random sampling. This cost doesn’t range from the testing charges, that are based on the exam lab.
Step Six: In parallel, you have to choose an authorized test lab for QTM testing by Lighting Global, and see using the lab aspects like availability and price of testing. To learn more, please review their list of approved test labs and also the Test Lab Policy.
Step 7: Return a signed copy from the Testing Agreement towards the QA team.
Observe that Random Sampling and Testing may start as we have obtained your completed Manufacturer Information Form along with a signed Test Agreement.
Step 8: Begin the payment procedure for the Program’s fee invoice and inform the QA team.
Observe that final testing recent results for your products(s) are only sent as we have confirmed payment of these charges.
Step 9: Complete the Random Sampling Form. This type asks that you simply: (A) Identify the specific test lab you’re considering to check your products(s), (B) Provide contact details for sampling, (C) Provide street address for that sampling location, and (D) Give a time frame for sampling.
Observe that finishing this type works as a confirmation that you’ll satisfy the minimum stock needs throughout the provided some time and location. Therefore, it’s very essential that all the details is finished and accurate.
Step 10: In parallel, your organization and also the lab must enter agreement for testing.
Observe that contracting and payment of testing charges is handled between your test lab.
Step 11: In the end the required information for sampling is received, the QA team arranges sampling by delivering the sampling information for an agent who’ll contact you to definitely schedule sampling and can then at random pick a needed quantity of samples from the specified stock number.
Step 12: Once samples are selected, it’s your responsibility to achieve the samples shipped towards the test lab and pay all connected shipping charges, responsibilities and taxes. To learn more browse the following program policy.
- Product Sampling Policy
Step 13: Once tests are complete, the exam lab transmits the exam results and draft test are accountable to the sunlight Global QA team for review.
Observe that test results sent straight to us through the client (you) won’t be considered valid.
Step 14: The QA team looks at the test report, determines if the product meets the needs from the Lighting Global Quality Standards, and verifies that charges towards the test lab and Lighting Global were compensated, before delivering the outcomes towards the manufacturer. To learn more, please browse the following program needs.
- Pico-PV Quality Standards
- SHS Package Quality Standards
- Performance Reporting Needs
When the product(s) DO satisfy the Quality Standards:
Step 15: The QA team drafts and offers a Standardized Specs Sheet (SSS) along with a Verification Letter (VL). To learn more about these supporting documents, please browse the following program guidelines and/or needs.
- Standardized Specs Sheet Description
- Standardized Specs Sheet Guidelines
- Communications and Branding Guidelines for Partners
Step 16: After your review and approval from the SSS and VL, the QA team starts coordinating the entire process of listing the merchandise around the Lighting Global website, and its Standardized Specs Sheet and Verification Letter. To learn more, look into the Online Presence stage from the Testing Process.
The Sunlight Global web site is the state site that confirms the validity of the product(s) Specs Sheet and Verification Letter, which your products is based on this program.
When the product(s) don’t FULLY satisfy the Quality Standards because of simple to fix issues that may be addressed without retesting:
Step 15: The QA team informs the maker that it features a “Conditional Pass” inside a letter that comes with the state test results. A conditional pass gives manufacturers an chance to create needed alterations in the merchandise packaging or documentation to satisfy the standard Standards. This kind of pass might be split into three groups: (A) Conditional Pass Pending Clarification, (B) Conditional Pass Pending Correction, and (C) Conditional Pass for Truth-in-Advertising around the Lighting Global Specs Sheet. Each category is treated differently, and so the needed changes and timeframes for every vary. For additional info on the entire process of items that get a conditional pass please browse the following program policy.
- Conditional Pass Policy
When the product(s) don’t satisfy the Quality Standards:
Step 15: The QA team informs the maker via email the product didn’t satisfy the Quality Standards, and describes the primary points of failure. In addition, the QA team features a “Feedback Letter” that explains the exam results and recommended next steps.
Key notes to think about:
Items that satisfy the Quality Standards might also make an application for Affiliate Status to get additional business services.
The Standard Test Method (QTM) answers are valid for 2 years. In that time, the merchandise might be susceptible to Market Check Testing.
QTM results might be restored for an additional 2 yrs. To learn more look into the Affiliate Renewal (AR) stage from the Testing Process and browse our Insurance policy for Renewing Test Results.
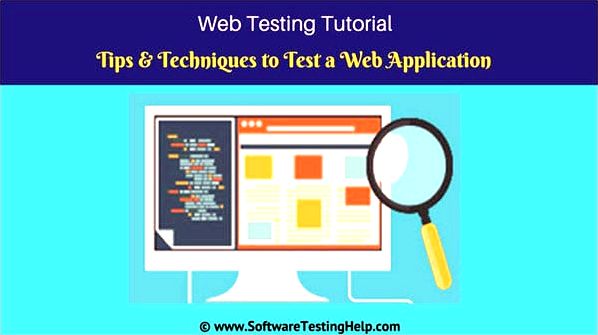
Your organization could make ongoing, incremental changes for your product. You need to alert us when these occur. When the changes to performance are small (e.g., creating a small update towards the Standardized Specifications Sheet), no further testing is going to be needed a status using the program. Large changes (generally, more than 10% improvement in performance) may need targeted re-testing a status.
Resourse: https://lightingglobal.org/quality-assurance-program/testing-process/quality-test-method-qtm-testing/